Net zero construction: the problem with embodied carbon
Published on 22nd October 2021
The UK government's Heat and Building Strategy fails to adequately address embodied carbon, which is expected to account for almost half of building-related emissions by 2060
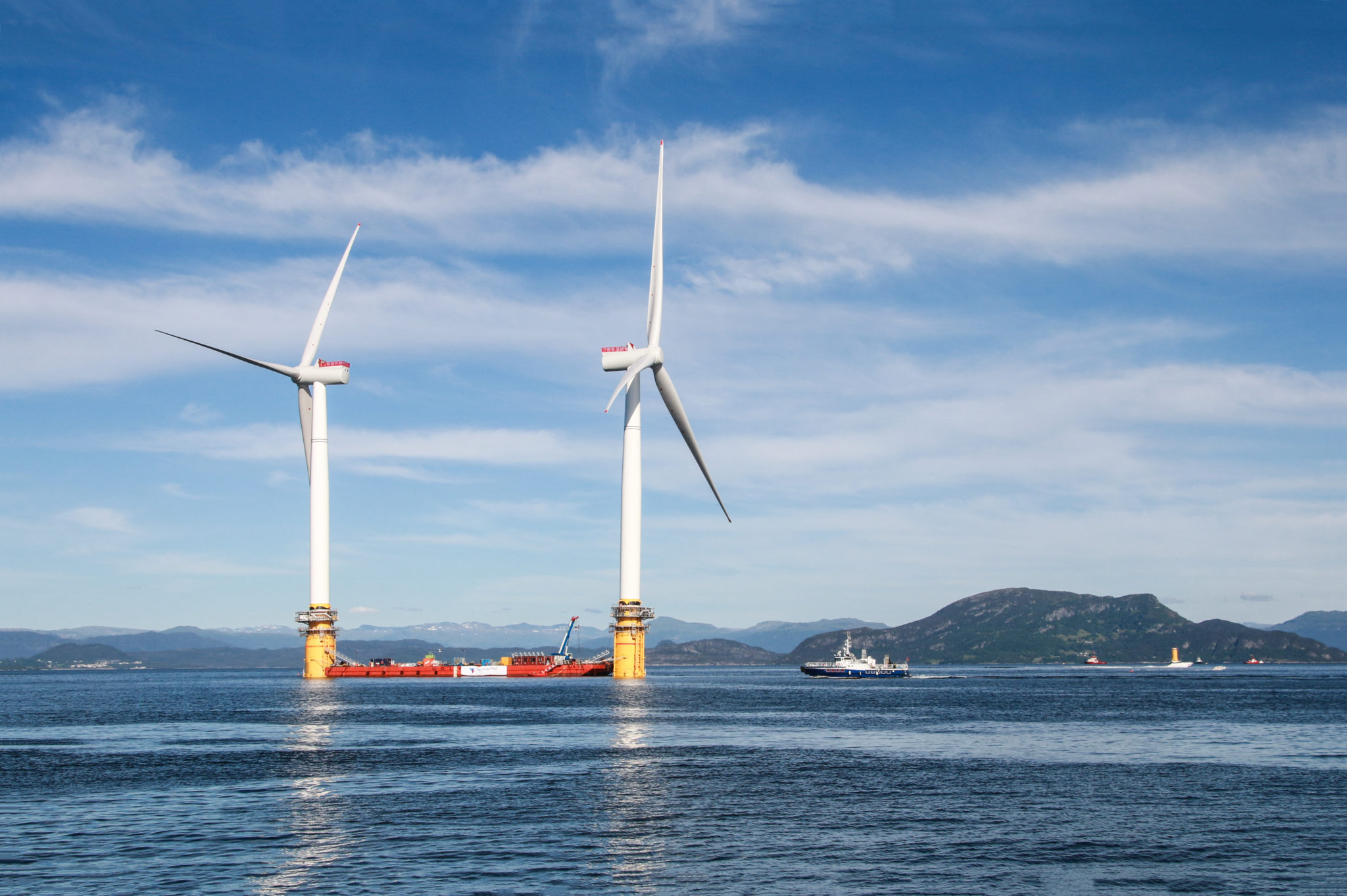
The UK government's broad commitment to "build back better" following the impact of the Covid-19 pandemic has been welcomed by a construction industry that has undergone more than its fair share of struggles in the past two years. However, detail around how the government plans to navigate the shift towards low-carbon construction and operation of the built environment in order to help achieve the government's emissions reductions targets (a 78% reduction from 1990's levels by 2035, net zero by 2050) has, until now, been limited.
In the long-awaited Heat and Building Strategy published this week, the government set out its plans to decarbonise the energy used to run and operate UK buildings day-to-day, known as operational carbon. While these proposals are to be welcomed, little was said about another important aspect of the problem of carbon emissions in the built environment: embodied carbon.
What is embodied carbon?
Embodied carbon refers to the carbon dioxide (CO₂) emissions associated with materials and construction processes throughout the whole lifecycle of a building project. This includes any CO₂ created during construction, including through the manufacturing of materials, the transportation of those materials, and the processes used to construct the building. It also encompasses the CO₂ produced in maintaining the building and eventually demolishing it and disposing of the waste. It does not include operational carbon.
According to the World Green Building Council, buildings are currently responsible for 39% of global energy-related carbon emissions: 28% from operational carbon, and 11% from embodied carbon. Global building stock is expected to double in size by 2060, at which point (on a business-as-usual projection) embodied carbon is expected to contribute almost half of overall building related emissions, given the increasing availability of low carbon options for meeting a building's operational energy requirements.
What can be done about it?
Existing buildings
Concerns about the high levels of operational carbon required to run old and poorly-insulated buildings in the UK has led to a general assumption that replacing existing building stock with energy-efficient replacements will reduce overall carbon emissions. However, industry specialists are now advising that, in most cases, retrofitting existing structures to increase their energy efficiency may be preferable given the embodied carbon involved in the initial construction of those structures, as well as the carbon cost of demolition. One example of this change in attitude can be found in the Architect's Journal's "RetroFirst" campaign which prioritises retrofit over demolition and rebuild. The campaign makes the point that "the greenest building is the one that already exists".
The energy efficiency measures intended to improve the operational emissions performance of existing buildings that were announced by the government in the Heat and Building Strategy can be seen as an acknowledgement that retrofitting existing buildings may often be preferable to the demolition and re-construction of existing buildings to higher standards. It remains unclear though whether the government has any plans to implement the changes advocated by campaigns such as RetroFirst, which call for regulation to make it harder for developers to demolish buildings, and incentivise the retrofitting of existing buildings where possible.
New buildings
Given the extent to which the built environment contributes to global carbon emissions, and the lack of government regulation on embodied carbon to date, it is perhaps not surprising that those operating within the construction sector are considering ways in which this substantial carbon footprint can be reduced.
One example of industry collaboration to change current practice is the proof of concept "Part Z" proposal to amend existing UK Building Regulations to mandate a whole life carbon assessment and limiting of embodied carbon emissions as part of the building design process. The proposal is supported by a number of industry operators. It aims to normalise the calculation, reporting and limitation of embodied carbon emissions at the outset of a qualifying construction project.
With the increasing onus placed on corporates to reduce their emissions, parties engaged on a construction project might wish to consider agreeing a carbon budget for a construction project within their contracts. One of the clauses published by the Chancery Lane Project, an initiative which aims to provide contractual solutions to climate change issues, has been designed for this purpose. The clause requires the contracting parties to agree a contractual carbon budget, and includes associated provisions to ensure progress against the budget is monitored and reported on by contractors. Though these clauses are not currently widely used in the market, they provide a useful framework for parties to discuss and consider including in their construction projects where the sustainability of a project is a significant concern for employers.
Materials
Mandating that carbon assessments are undertaken is only the first step in a long and difficult journey to realising a substantive reduction in a building's overall carbon footprint. The need for low carbon construction materials, at commercially sensible prices, is an obvious and substantial hurdle to reducing the carbon footprint of the construction industry.
The manufacture of building materials makes up around 11% of total global greenhouse gas emissions (according to data from the United Nations Environment Programme) and it is understood that cement is the source of about 8% of the world's CO₂ emissions (according to think tank Chatham House). Low carbon cement and concrete alternatives have been acknowledged in a recent report from Economist Impact, commissioned by Osborne Clarke, as one of the top 12 decarbonising technologies for cities. The report notes that there is currently little investment in low carbon cement and concrete alternatives, despite their scalability given the widespread availability of the raw materials. It is apparent that significant investment and innovation in these materials will be required in order to reduce the emissions footprint of the industry.
The need to reduce the carbon cost of construction materials is also receiving increasing recognition in the industry. The Global Cement and Concrete Association has recently announced a roadmap to achieve net zero emissions in the sector by 2050, with the backing of some of the world’s largest cement companies. While delivering on this pledge will be challenging (given that CO₂ production is integral to the very process of creating cement, which is a key ingredient in concrete) it will have a crucial role in helping to achieve net zero, with research and development teams working to deliver a wave of innovative concrete solutions and developing lower-carbon, higher performance, lightweight concretes of the future.
Osborne Clarke comment
Embodied carbon represents a significant challenge to UK net zero emissions, both in terms of the extent of its contribution to total emissions, and the difficulty in reducing them.
Though the Heat and Building Strategy includes detail on the government's plans to reduce the operational carbon emitted as a consequence of heating UK buildings, there is a notable absence of consideration of embodied carbon in the strategy.
The government's wider Net Zero Strategy does, however, reference plans to support action in the construction industry by improving reporting on embodied carbon in buildings (with a view to exploring a maximum level for new builds in the future) and recognises the potential to reduce embodied carbon by way of material substitution, where appropriate. Though these acknowledgments are to be welcomed, the lack of detail around the proposals concerning embodied carbon is disappointing, as many in the industry had hoped that this issue would be comprehensively addressed in the strategy.
As government and businesses increasingly focus on reducing carbon emissions, we anticipate a gradual shift towards the introduction of carbon budgets (alongside financial budgets) on construction projects in order to help achieve a reduction in emissions across the life-cycle of a construction project – whether these budgets are mandated by the government (with potential penalties for noncompliance), or introduced by parties to a construction project who are keen to reduce and closely monitor their carbon emissions. This shift is likely to necessitate the increased uptake of lower carbon building materials which, despite demonstrating huge potential in reducing carbon emissions, are in need of significant investment in order for that potential to be realised.