The future of the construction industry: offsite construction, next-generation connectivity and artificial intelligence
Published on 17th May 2021
In this Sector note, Osborne Clarke LLP discuss how new and emerging technologies (such as next general connectivity and artificial intelligence (AI)), and modern methods of construction (MMC) (such as offsite and modular construction), may change the construction industry in the years to come.
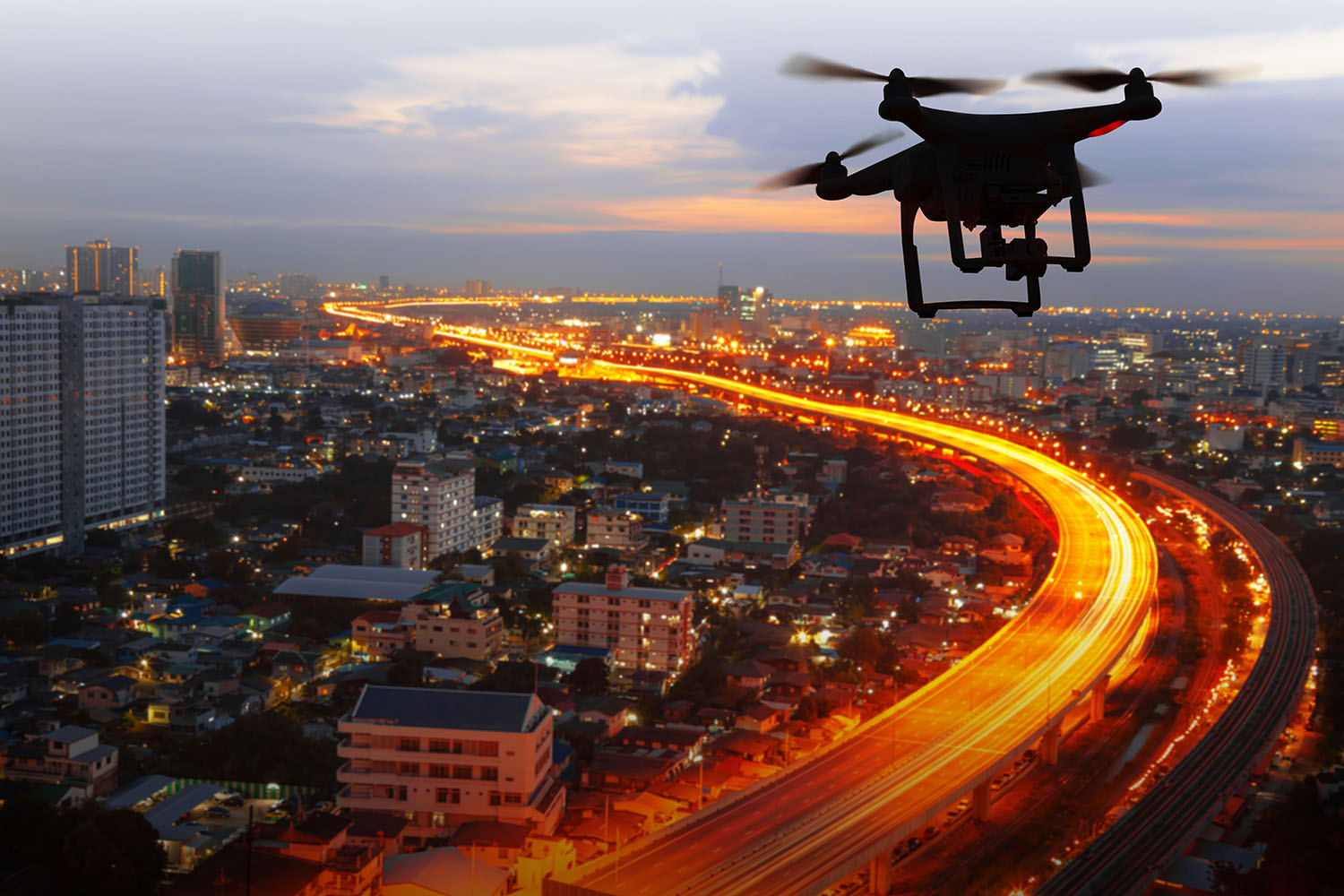
Scope of this note
This note discusses the future of the construction industry and the ways in which new and emerging technologies and modern methods of construction may shape the industry.
Current challenges for the industry
The difficulties facing the construction industry have been well publicised. Reports including the 2016 Farmer Review have identified the following major challenges for the industry:
- Low productivity levels. A 2019 report by Turner & Townsend reported that in almost three decades, productivity in the construction industry has increased by just 14.8%, compared to approximately 47% for services and over 90% for manufacturing.
- Low predictability. Delays and cost overruns are perceived as an all-too-common feature of projects from the complex and simple.
- Structural and leadership fragmentation. According to research by the Chartered Institute of Building (CIOB), more than three-quarters of construction professionals believe the industry's current management of quality is inadequate.
- Low margins. Low margins are an ongoing historic challenge, as too often contracts are awarded based on the price alone. As the 2016 Farmer Review put it, "whoever wins a project is often the party that has made the largest mistake in pricing it!".
- Adversarial pricing models. Competitive tendering has ingrained into the industry an adversarial and "blame-game culture" with little use of collaborative or incentivised commercial engagement or early engagement with other stakeholders.
- Financial fragility. Razor-sharp tendering by lead contractors puts at risk not just those companies, but the extensive and diffuse supply chains that rely upon them.
- Workforce size and demographic. A shrinking labour pool is exacerbated by the construction industry lagging behind other industries in improving the diversity of the workforce.
Innovation and cutting-edge technology offer a solution to these challenges. However, construction companies have been shown to overlook the availability of technology and its associated benefits, often due to the expensive upfront capital investment required The low uptake of R&D tax reliefs in the industry is reflective of a lack of awareness that the business is in fact undertaking R&D and the fiscal assistance available.
Technology within the industry is only going to become more prevalent and it is likely that the adoption of digital methods to improve efficiency and profitability will prove crucial in allowing companies to remain competitive. This Sector note investigates three categories of construction technology or "ConTech" and how they might mitigate or circumvent the issues facing the industry.
Offsite and modular construction
"Prefabricated", "offsite" or "modular" construction is far from a new concept. Many will be familiar with prefab buildings that proliferated in the UK in the post-war era, but while these buildings went out of fashion in the second half of the twentieth century, recent technological advances have put offsite and modular construction firmly back into the spotlight.
The benefits of offsite construction
At their heart, many of the challenges facing the construction industry relate to the on-site environment, where the opportunities for automation and standard processes are relatively limited; the weather is unpredictable (especially in the UK); and, fundamentally, no two builds are the same.
Offsite construction can alleviate many of these issues:
- Offsite facilities can be equipped with other new technologies. Taking construction offsite and into a manufacturing environment opens the door to standardised designs, streamlined processes and automated production techniques incorporating advanced robotics and the Industrial Internet of Things (IoT).
- Reduction in build time. A National Audit Office report from 2005 found that offsite construction methods could reduce onsite build time for housing by half and require less on-site labour. In April 2021, the offsite construction of a hospital ward at North Middlesex Hospital worth almost £2 million reduced the onsite construction time from ten weeks to six.
- Reduction in risk of time and cost overruns. With modular construction simplifying the design process and production techniques standardised, the risk of time and cost over-runs is greatly reduced, providing more stability across the supply chain. Offsite construction greatly simplifies contract management and reduces the opportunities for disputes to arise.
- Increased safety for workers. Working from height, unintended collapses, moving objects and vehicles as well as materials handling are some of the most common causes of injury. The greater the proportion of work that takes place in a controlled, predictable environment, the safer the industry will become.
- Less waste. Offsite construction also typically produces less waste. Design for manufacture and assembly (DfMA) enables materials to be calculated with a high degree of precision. Likewise, 3D printing, as an additive process, requires only the material that is actually needed for the build. With sustainability an increasingly important driver for regulation, not to mention brand, techniques that reduce waste will increasingly be a priority.
- Versatility. Offsite construction is not just for off-the-shelf solutions. In 2019, the largest 3D printed concrete bridge opened in Shanghai. The build incorporated other technologies such as robotics (with two robotic arms being used to print the structure offsite) and the IoT, with embedded sensors providing real-time data on vibration and stresses on the bridge. Such projects are a far cry from the prefabs of the 1950s.
What are the potential drawbacks?
The uptake of offsite construction has been modest; this is in large part due to the cost of setting up the facilities initially required. With technological advancements coming rapidly, there remains the risk of more advanced plants becoming available on the market for an equivalent or lower price, making companies loath to make the investment commitment when more cost effective solutions could be around the corner. The question to be asked by companies is whether the potential benefits justify the cost, and whether the business has the capacity and appetite to make that sort of investment. As the Farmer review put it:
"much of the industry does not make enough money, or, where money is being made, feel enough confidence it will stay profitable into the future. The consequence is underinvestment in training and development, in innovation, in raising productivity."
In an industry of low margins, at a time when project pipelines are unclear or uncertain, businesses tend to take a project-by-project approach, rather than committing major investment for long-term returns. The industry faces a "chicken and egg" scenario where, while offsite construction requires high volumes in order to be profitable, demand will only increase once offsite construction is a more mainstream offering.
A further concern on the part of clients is that on offsite approach may restrict architectural design ambition. While the versatility of the application of offsite techniques has already been discussed, and although a speedier process brings with it significant benefits, particularly on costs, a perceived reduction in freedom of design frustrates a project's key area of differentiation and the standardisation associated with offsite builds can be viewed as a barrier to architectural brilliance.
It will take more projects akin to Lister's Pods (penthouse apartments placed on a 19th century Bradford mill) or March House (a Thameside stilt house) to give such clients confidence that offsite construction can go hand-in-hand with bespoke architectural designs. Once again, however, for these fears to be allayed, a greater volume of eye-catching, offsite constructed projects need to hit the headlines, which is less likely to happen while clients are wary and no impetus is given.
The solution: government-led or industry-led?
Some argue that with a third of all construction projects being ultimately funded by government, the government has the means and motivation to break the deadlock, so should be incentivising offsite construction.
Certainly, the government claims to be committed to modern construction methods when it comes to building homes, and has introduced a presumption in favour of offsite construction and offsite forms a major part of the Construction Sector Deal launched by the government in July 2018. Departments such as Education and Justice have awarded 23 contracts with offsite components. For example, in January 2020 the Department for Education launched a £3 billion framework for modular schools in England. To meet the demand for Covid-19 test centres, the Department for Health and Social Care commissioned modular buildings across 50 sites in the UK. Given that the government are committed to adapting construction methods to reflect technological advancement, the number of contracts involving offsite construction is likely to increase.
This strategy appears to be coupled with a reform in procurement model (the government's recently-published green paper indicates that change is coming, with contracting authorities set to be encouraged to take a broader view of what constitutes value for money, such as social value. The reform will place greater emphasis on innovation and efficiency, rather than just price, which could hopefully incentivise modern methods of construction. It should also promote and develop collaborative regional frameworks to give contractors and their supply chain the certainty and confidence to invest in R&D. The fear is that, if not implemented correctly, the Construction Sector Deal will simply focus on value for money and further fuel the industry's "race to the bottom" mentality.
Despite five government departments committing to prioritise offsite construction, in 2019, two of those departments (Transport and Defence) procured no contracts with an offsite component. Since then, progress across these and the Department for Health and Social Care has been slow. The 22 contracts awarded by the Department of Education in 2019 show an inconsistent approach from the government.
To really make a difference, offsite construction needs to be embraced by industry. The Farmer Report offers some suggestions, such as promoting factory-sharing, centres of excellence and collaboration and promoting "innovation hubs". Several key players are making these moves, including Tier 1 contractors, employers and developers, but these are the exception rather than the norm.
A more radical approach would be to move away from traditional cost models based on capital expenditure and incorporate a new measurement of pre-manufactured value (PMV). Specific priority should then be considered for high PMV solutions – which could link back to government, through the way that costs are assessed in procurement exercises.
Ultimately, if this is something that clients want, the industry will move to satisfy that demand. On this measure there is perhaps encouragement that clients may be ahead of contractors. Research from Loughborough University found that a greater proportion of clients (73%) were aware of the benefits and challenges of offsite construction than contractors (54%) (Chris I Goodier and Alistair GF Gibb: Barriers and Opportunities for Offsite in the UK and Future opportunities for offsite in the UK).
Next generation connectivity
There is a great deal of excitement around next generation connectivity, and 5G in particular. It promises extremely fast speeds for data management, improved reliability and increased capacity. 5G's greater bandwidth and lower latency enable very fast relay of large amounts of data back to the cloud (or central servers) for processing and analysis, with a near real-time return of the outputs. Cloud computing also typically opens up the possibility of far more complex processing being undertaken because of the extent of the processing capacity and tools available in the cloud.
The benefits for the construction industry
Capturing and analysing data is increasingly important to enable successful construction project delivery. 5G enables real-time data capture and analysis on projects, meaning that decisions can be made almost instantly and issues rectified swiftly.
Real-time decision making: the knock-on effects
Photos and videos are typically used to complement written reports to detail progress. They highlight dangers on site; and they are often used retrospectively to justify claims for additional time/money or if matters turn litigious. 5G connectivity and other new technologies could interact to automate numerous stages of this process. For example:
- A project team could use a drone to record footage of the work on site, or capture data through wearable tech (such as sensors) on hi vis jackets or helmets.
- This data builds up an accurate "as built" picture of the works.
- 5G and systems based on AI could see automatic decision making based on the data produced (using a set of pre-determined rules).
- Once such a decision is made, the works could be automatically re-sequenced to identify behind-programme activities.
- The decision may then be fed into software that determines whether there is a viable claim, which then triggers notices of claims to be issued in accordance with the contract.
With next-generation connectivity, all of this could be done (almost) simultaneously.
The cumulative effect of automating the process in this way would be a large time-saving for the workers, who do not have to wait for photos to upload, or have to piece progress reports together. Their time could be spent instead focusing on the less administrative side of project management. However, in addition to adopting next-generation technologies, such seamless integration as described above is also reliant on adequate project management and collaboration software.
Simplification of legal issues
Using 5G technologies in this way could also simplify the legal aspects of a construction project.
For example, given that next generation connectivity can help to create a much more accurate and fact-driven picture of progress on site, there may be less reliance on subjective documents like progress reports and meeting minutes when reflecting on "what happened, and why". This may be particularly helpful for those making or facing a delay or disruption claim. In the long-run, this could reduce the overall number and cost of disputes, perhaps allowing parties to move to a data-driven process for resolving claims.
Issues to watch out for
There are a number of areas in which industry practice and the law will need to develop in order to manage the increasing use of technology and 5G on construction sites, and the vast amounts of data that would be gathered through adopting these methods.
The legal aspects mirror those in many other industries, and centre on the processing and security of large amounts of data. For example:
- Cybersecurity. What are the potential liabilities if the data is hacked?
- Disclosure. More data may also result in more data being processed, stored and analysed as part of any disclosure process in litigation or arbitration.
- Ownership of and responsibility for data. Who "owns" the data captured: the client, the contractor or the sub-contractor? Contracts will need to be amended or supplemented with agreements dealing with the governance of, access to and protection of data, to deal with issues like:
- how data protection legislation will be followed if, for example, footage is captured of a person who does not consent, or a photo of a neighbouring property; and
- how to deal with responsibility for notifying the relevant authorities of unsafe or illegal activity recorded on site by a drone.
Industry participants will also have to consider:
- Interfaces. How will they make sure that data collected is being used effectively? For example, interfaces need to be designed such that the data can be applied to solve problems, and does not bog a project down. Data produced by drones, for instance, should lead somewhere (such as a re-sequenced programme of works, assessment of payments for work done or triggering early warning notices), rather than being gathered for no positive purpose.
- Integration. Some of the potential benefits will not be realised if systems across the supply chain are not integrated. While sophisticated clients or contractors may benefit, parties elsewhere in the chain, who may still be reliant on paper-based systems, might not be able to process and cope with new data streams.
Artificial intelligence
Next generation connectivity is a pre-requisite for the application of AI. From VR headsets that show different built options, to construction workers controlling machines from their homes during lockdown, the breadth of application of AI to the construction industry is both impressive and challenging.
Use of AI in the construction industry
Some examples of AI adoption include:
- Building information modelling (BIM). While BIM is not in itself a form of AI, AI can be used in conjunction with BIM to flag problems or allow collaborative working such as assisting with the design process.
- Facial recognition. This can use AI technology to confirm that workers are on the payroll and monitor who is coming in and out of a construction area, in order to reduce security risks.
- Data analytics. AI can analyse the large volumes of heterogeneous data produced on construction projects, which is expected to increase exponentially as technologies such as sensor networks and the IoT are commoditised.
- Sensor networks and IoT. These can be used in tandem with AI to implement a network of interrelated devices and machines with the ability to transfer data over a network without requiring human interaction. On construction projects, their benefits include reducing accidents: digital solutions such as sensors on workers' clothing and hardhats monitor for hazardous materials and could alert workers to risks before they enter unsafe site areas.
- Budgeting and project monitoring tools. These use AI to forecast outcomes and can predict the knock-on impact of issues and overspend, write financial reports, recognise defects and assist with completion sign-off.
The benefits of AI
AI offers the potential for improved efficiency, increased productivity and reduced costs. However, the adoption of new technology raises its own questions: is personal data being handled and analysed properly, are jobs at risk, and is there a risk that profit is being pursued at the expense of safety?
The experience from other sectors suggests that some of these big-picture fears are unfounded. Job roles are likely to be changed rather than lost, as people have a crucial role to play in directing and implementing new technologies. AI could also produce safer sites, removing the requirement for people to undertake dangerous aspects of work, alerting workers of key hazards and identifying potential defects before they occur.
Managing the risks
Construction projects are incredibly complex and require highly skilled workers to get them over the line. The balance between use of people and AI needs to be carefully considered, alongside their risk profiles, to maximise the practical and financial opportunities for the industry.
It is essential before implementing new technology, such as AI, that the legal, regulatory and practical risks are fully understood and mitigated. Some of the key legal issues that must be faced are described below.
Ownership
It is crucial to establish at an early stage who will own the data, know-how or other intellectual property derived from the new technology, and who will take responsibility for its commercialisation.
Clients, contractors and sub-contractors often partner with software development companies or start-ups in the race to harness the benefits of AI in the construction industry. This can lead to disputes over the ownership of commercially valuable technologies, particularly where a party has contributed significant sums to the cost of the project, only to find that they do not have appropriate rights in the end product.
Data protection
In order to adapt, machine learning requires large datasets to analyse and train upon. Some implementation models allow users to effectively "rent" a dataset upon which to train their own systems. Other users prefer to insource their systems, or use AI as a service. In any event, care must be taken before collecting, sharing and processing personal data.
Failure to comply with data protection legislation could lead to criminal prosecution and significant fines. Use of AI in facial recognition, sensors or other methods of monitoring individuals on a construction site, for example, could lead to issues in processing data. Developing practical policies for managing data and dealing with subject access requests will minimise risk.
Cybersecurity
The risk of a cyber-attack is evident, given the significant amount of personal data that can be collected and processed within a construction project, as well as the payments being made in connection with the project and the potential for ransomware to disrupt time-sensitive actions.
Supply chains play a vital part in the security, or vulnerability, of the end system. Industry participants should ensure that appropriate due diligence has been carried out on suppliers and that contracts contain adequate cyber-security protections and audit rights.
There are tight timescales for reporting data breaches. It is advisable to put in place a response policy and ensure all relevant individuals are aware of the steps that need to be taken.
Licensing
Industry participants should take care when entering into licences to use technologies within the construction environment. Checks should be carried out to ensure that rights of use can be assigned or sub-licensed to sub-contractors, to allow collaboration across design and build.
Liability
Collaboration through AI systems can also lead to difficulties in establishing who has responsibility for issues. For example, who has a duty to warn where multiple parties have inputted to the design?
Risks must be identified, with appropriate insurance and contractual liability flow-downs to ensure that the costs associated with any liabilities do not impact on the viability of the project.
Changes to the regulatory framework should also be closely monitored, as legislators approach liability issues in relation to AI.
Reproduced from Practical Law with the permission of the publishers. For further information visit www.practicallaw.com
by Daniel Cashmore, Tom Andrews, James Walsh and Becky Crawford