Offsite and modular construction: will the digital revolution be built off-site?
Published on 25th February 2020
Welcome to the first article in our series on construction technology. We will be publishing regular further articles on a host of other topics including next-generation connectivity, AI and robotics.
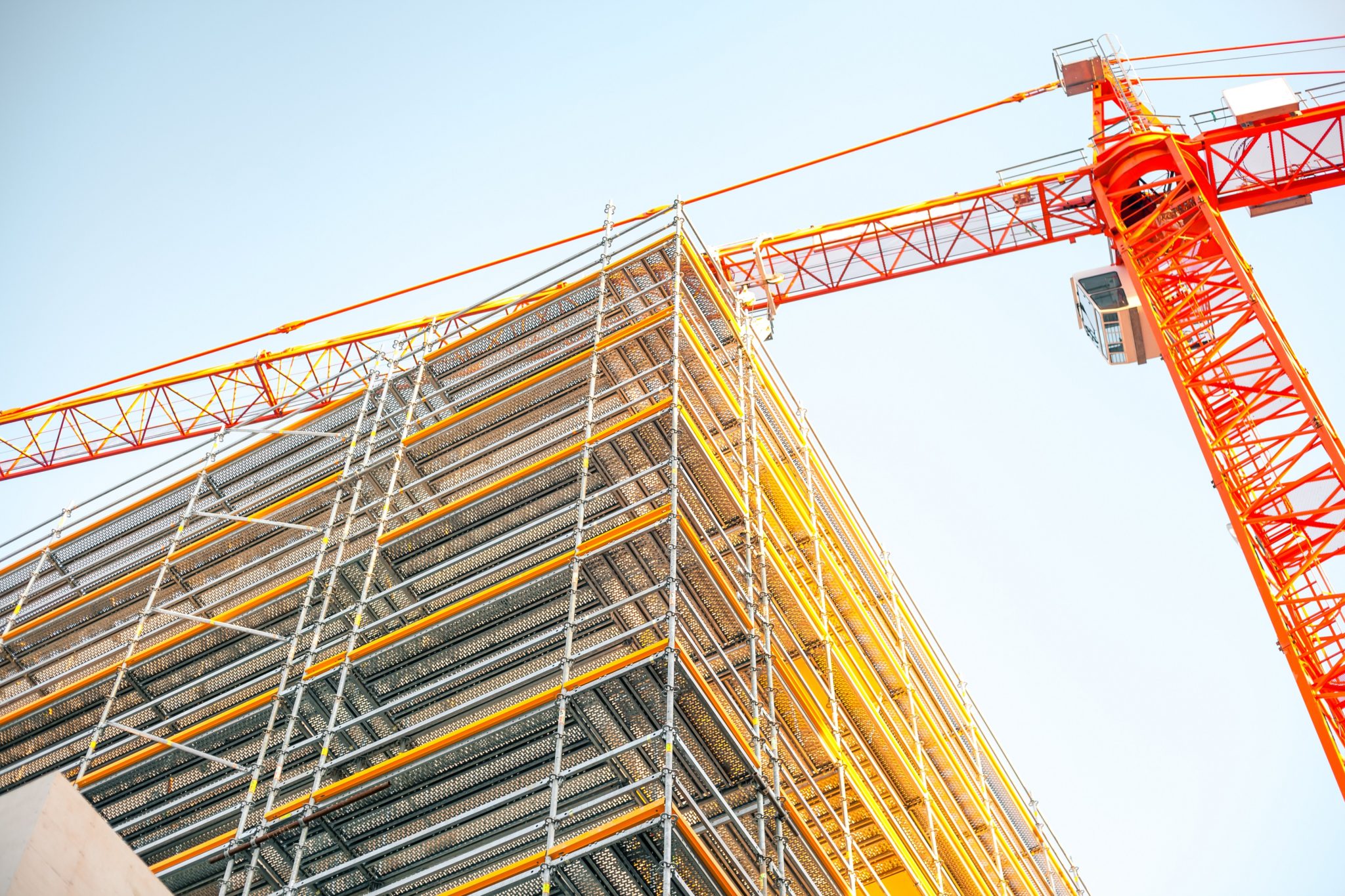
In Hyde Park, a structure is being brought in to host a Great Exhibition of the latest technology. It has been assembled offsite and after the exhibition will be taken apart and moved to another site to be re-assembled. 9,000 miles away, in Changsha, China, a 57 storey building is being built at lightning speed, with the total build taking just 19 days.
The two projects are separated not just by distance but also by time – Crystal Palace in London was built in 1851; Mini Sky City in China in 2015. But the two projects have one important thing in common: they were both built utilising the latest (for their time) techniques in off-site construction.
Prefabricated / offsite / modular construction is far from a new concept – many will be familiar with prefab buildings that proliferated in the UK in the post-war era, a century after Crystal Palace. But whilst prefab buildings went out of fashion in the following decades, recent technological advances have put offsite and modular construction firmly back into the spotlight. According to proponents, offsite construction is an answer to many of the challenges currently facing the construction industry.
What are those challenges?
The difficulties facing the construction industry have been well publicised. The Farmer Review, amongst others, has identified the following major challenges for the industry:
- Low productivity levels: a report by WPI economics found that productivity in the construction industry had increased by just 10% in 20 years, compared to 30% across all sectors.
- Low predictability: delays and cost overruns are perceived as an all-too-common feature of projects from the complex (e.g. Crossrail) to the everyday.
- Structural and leadership fragmentation: according to research by the CIOB last year, more than three-quarters of construction professionals believe the industry's current management of quality is inadequate.
- Low margins: low margins have plagued the construction industry for decades, as all too often contracts are awarded based on the price alone – or, as put in the Farmer Report "whoever wins a project is often the party that has made the largest mistake in pricing it!"
- Adversarial pricing models: competitive tendering has ingrained into the industry an adversarial and "blame-game culture" with little use of collaborative or incentivised commercial engagement or early engagement with other stakeholders.
- Financial fragility: razor-sharp tendering by lead contractors puts at risk not just those companies, but the extensive and diffuse supply chains that rely upon them.
- Workforce size and demographic: a shrinking labour pool is exacerbated by the construction industry lagging behind other industries in improving the diversity of the workforce.
How can offsite construction help to meet these challenges?
At their heart, many of the challenges facing the construction industry relate to the on-site environment. The opportunities for automation and standard processes are relatively limited, the weather is unpredictable (especially in the UK) and, fundamentally, no two builds are the same.
Offsite construction can alleviate many of these issues. Taking construction offsite and into a manufacturing environment opens the door to standardised designs, streamlined processes and automated production techniques incorporating advanced robotics and the Industrial Internet of Things (IoT).
A National Audit Office report from 2005 found that off-site construction methods could reduce onsite build time for housing by 50% and require less on-site labour. More recently, BRE innovation site has shown that a house can be built in just one day. And with modular construction simplifying the design process and production techniques standardised, the risk of time and cost over-runs is greatly reduced, providing more stability across the supply chain. The nature of projects is such that disputes will always be a feature of the construction industry, but off-site construction greatly simplifies contract management and reduces the opportunities for disputes to arise.
There are other ancillary benefits. The industry has come a long way when it comes to health and safety but construction remains one of the most dangerous sectors to work in and injuries and, sadly, fatalities are still commonplace. Working from height, unintended collapses, moving objects and vehicles as well as materials handling are some of the most common causes of injury. The greater the proportion of work that takes place in a controlled, predictable environment, the safer the industry will become.
Off-site construction also typically produces less waste. Design for manufacture and assembly (DfMA) enables materials to be calculated with a high degree of precision. Likewise, 3D printing, as an additive process, requires only the material that is actually needed for the build. With sustainability an increasingly important driver for regulation, not to mention brand, techniques that reduce waste will increasingly be a priority.
And off-site construction is not just for off-the-shelf solutions. Last year, the largest 3D printed concrete bridge opened in Shanghai. The build incorporated other technologies such as robotics – with two robotic arms being used to print the structure offsite – and the IoT, with embedded sensors providing real-time data on vibration and stresses on the bridge. A far cry from the prefabs of the 1950s!
So what's holding the industry back?
As the manufacturing industry knows only too well, there will always be more advanced plant available on the market, which could improve production. The question is whether the potential benefits justify the cost, and whether the business has the capacity and appetite to make that sort of investment. As the Farmer review put it:
"Put simply, much of the industry does not make enough money, or, where money is being made, feel enough confidence it will stay profitable into the future. The consequence is underinvestment in training and development, in innovation, in raising productivity."
In an industry of low margins, at a time when project pipelines are unclear or uncertain, businesses tend to take a project-by-project approach – rather than committing major investment for long-term returns. Leo Quinn, the Chief Executive Officer of the UK's largest contractor, Balfour Beatty, has said that the industry is "held back by the significant upfront investment needed (in a low margin sector) and the limited profitability of offsite while the mark for it remains narrow. Clearly something needs to be done to incentivise the sector to create capacity now for when it is needed."
There is the chicken-and-egg problem that the profitability of off-site construction requires high volumes, but the demand will only come once offsite construction is a more mainstream offering.
Clients remain hesitant on using an offsite approach on their projects through fears that it will restrict architectural design ambition. Standardisation and factory manufacture represent, for many, barriers to architectural brilliance. While a speedier process brings with it significant associated benefits, particularly on costs, a perceived reduction in freedom of design frustrates a project's key area of differentiation. For such clients, it will take more projects akin to Lister's Pods (penthouse apartments placed on a 19th century Bradford mill) to give them confidence that offsite construction can go hand-in-hand with architectural excellence. The chicken-and-egg returns however, as for fears to be allayed, a greater volume of eye-catching, offsite constructed projects need to hit the headlines, which is less likely to happen while the fears exist and no impetus is given.
The solution: government-led or industry led?
Some argue that with a third of all construction projects being ultimately funded by government, the government has the means and motivation to break the deadlock, so should be incentivising off-site construction. Certainly the government claims to be committed to modern construction methods when it comes to building homes, and has introduced a presumption in favour of off-site construction. It also forms a major part of the Construction Sector Deal launched by the government in July 2019. Departments such as Education and Justice have awarded 23 contracts with offsite components. For example, recently Laing O'Rourke and Wates were named among other winning contractors on the Department for Education's £3bn modular schools framework for England. The number of these types of contract offering an offsite component would be expected to increase given that the government have said they are committed to adapting construction methods to reflect technological advancement.
However it is unclear whether this strategy will be coupled with a change in procurement model towards a more risk sharing approach on projects which incentivises modern methods of construction. It should also promote and develop collaborative regional frameworks to give contractors and their supply chain the certainty and confidence to invest in R&D. The fear is that, if not implemented correctly, it will simply focus on value for money and further fuel the industry's 'race to the bottom' mentality.
Despite five government departments committing to prioritise offsite construction, within the first eight months of last year, three of those departments (Health, Transport and Defence) procured no contracts with an offsite component. The 22 contracts awarded by the Department of Education paper over the cracks of inconsistency in approach from the government. Mark Farmer's appointment as the national MMC (modern methods of construction) adviser may help to align the government's approach. His main criticism of the government departments that committed to the presumption in favour of offsite is that they lack the necessary intelligence to implement it in procurement and need "re-educating around how you procure value and how you actually deploy the MMC presumption in a way that achieves end value".
To really make a difference, off-site construction needs to be embraced by industry. The Farmer Report offers some suggestions, such as promoting factory-sharing, centres of excellence and collaboration and promoting "innovation hubs". We are seeing this move by some Tier 1 contractors (e.g Laing O'Rouke, Mace and Balfour Beatty), Employers (e.g. Heathrow's commitment to offsite construction, including its Logistics Hubs) and also Developers (e.g. L&G's modular homes), but these are unfortunately the exception rather than the norm.
A more radical approach would be to move away from traditional cost models based on capex and incorporate a new measurement of pre-manufactured value (PMV). Specific priority should then be considered for high PMV solutions – which could link back to government, through the way that costs are assessed in procurement exercises.
Ultimately, if this is something that clients want, the industry will move to satisfy that demand. On this measure there is perhaps encouragement that clients may be ahead of contractors. Indeed,research from Loughborough University found that a greater proportion of clients (71%) were aware of the benefits and challenges of off-site construction than contractors (54%).
While the drivers for change are still unclear, in common with other areas of ConTech, such as BIM level 2, contractors need to be bold and embrace change or face being left behind and becoming irrelevant. We are working with businesses across a range of sectors to understand the challenges posed by new technologies and develop their digital transformation strategy.
If you would like to discuss how we can help, please get in touch with one of the experts listed below, or your usual Osborne Clarke contacts.